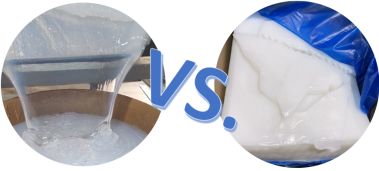
People familiar with silicone are aware of its two states: liquid and solid. What distinguishes these states from each other? What advantages do they have?
Concept
As its name suggests, liquid silicone is in a liquid form, which offers the benefit of excellent flowability, exceptional clarity, and rapid curing.
Solid silicone is solid and has no fluidity at ordinary temperatures. Solid silicone is a transparent elastic polymer material, which has the characteristics of high temperature resistance, cold resistance, solvent resistance, corrosion resistance, adhesion resistance, electrical insulation , etc., and has a wide range of applications.
Processing methods
Liquid silicone is typically injection molded, which involves injecting liquid silicone into a mold and allowing it to cure. The process flow of injection molding is relatively simple. Accurately measure the exact proportions of adhesive A and adhesive B, and carefully place them in an injection device for thorough mixing. The resultant mixture can then be injected into a heated mold. These processing methods belong to sealed feeding molding.
Solid silicone, on the other hand, is typically compression molded. Its raw materials are solid parts. After mixing, the cutting machine precisely cuts the products into suitable sizes and thicknesses. Next, placing them in molds and compressed at a specific temperature by a pressure molding machine. These processing methods belong to open feeding molding.
How to distinguish liquid silicone from solid silicone products?
Generally, liquid silicone products have higher transparency, but products have glue injection ports. Solid silicone products do not have injection ports for adhesive.
In conclusion, both liquid and solid silicone have their advantages and have a wide range of applications. Understanding the differences between the two forms of silicone can help you choose the right material for your specific application.