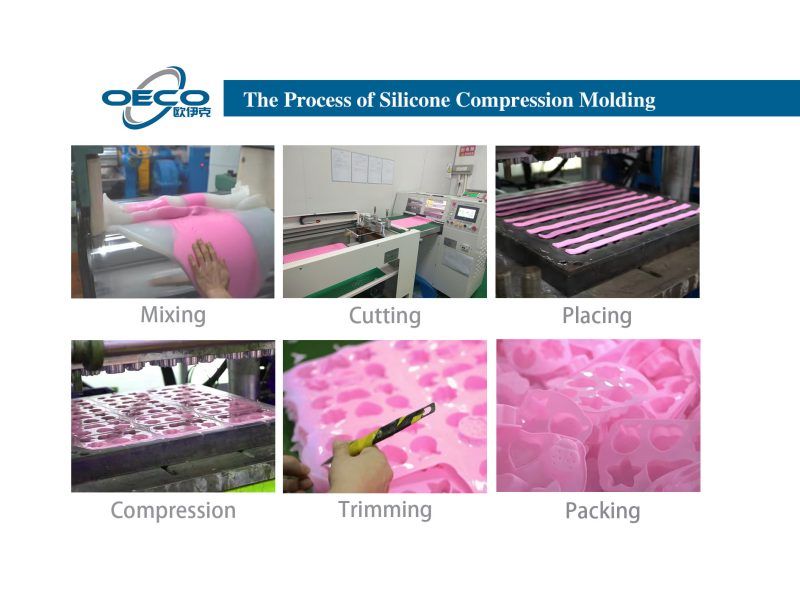
With the development of technology, silicone products are constantly improving in quality, leading to their increased application in various industries. Different silicone products have different manufacturing processes. Today, OECO will introduce the most common production methods- compression molding.
The compression molding process of mainly includes: raw material preparation – cutting – pressing – trimming – inspection – post-treatment – inspection – packaging.
1, Preparation of the silicone material: Mixing raw silicone material with additives and pigments to achieve the desired properties and color. The mixture is then heated and mixed until it becomes a homogeneous mass. The general mixing time is about 30 minutes. P.S. the time is determined according to the weight of raw materials and the gap between rollers.
2, Cutting: Cutting machine precisely cuts the products into suitable sizes and thicknesses. Then let them stand for a period of time. The general standing time of raw materials is about 8 hours. Cover PE molds in both sides of raw materials to ensure the cleanliness of raw materials;
3, Transfer of silicone material to the mold: Placing silicone material into the mold, and closing the mold.
4,Compression: Applying Heat and pressure to the mold to compress the silicone material. The heat causes the material to soften and flow, conforming to the shape of the mold.
5, Mold opening and burrs removal: The mold opening, and removing the newly formed product. Processing with burrs for qualified products.
6, Inspection and trimming: Inspected for defects and trimmed for if necessary.
7, Post-treatment: Some products need surface oil spraying, printing, laser engraving and other processing.
8, Secondary inspection: Inspected for defects of product.
9, Packing
The finished product is typically a high-quality, durable, and reliable component that meets the required specifications and standards.